Saving water
The manufacture of lines and machines and operation of beverage filling and packaging systems always consume energy and media. Cutting down on the amount used is one of the most important objectives of our sustainability strategy. Reducing water consumption in particular is a chief area of focus.
Drinking water is an essential precious commodity. The United Nations have made it one of their top objectives to try and ensure the supply of clean water worldwide. It is thus a great aim to reduce the consumption of fresh water for industrial purposes in as far as we can. For many years we have been developing systems to this end for our customers’ turnkey lines and will lend even greater weight to this task in the future.
Our water footprint is an important indicator of the amount of water consumed in this respect. This refers to the amount of water a company (or a nation or a consumer) uses – and not just directly but also indirectly. This is calculated by also taking into account the quantity of water required to manufacture the products used, such as machines. For us as a company our water footprint is thus relevant in two ways: in reducing our water consumption we not only influence our own water footprint but also that of all customers who use our systems.
The more efficiently our machines are manufactured and run and the less water used in the production and operation thereof, the smaller the water footprint of those who operate them.
The more efficiently our machines are manufactured and run and the less water used in the production and operation thereof, the smaller the water footprint of those who operate them. This is one more incentive for us to work on innovative, resource-saving systems which increasingly focus on water consumption in particular. This applies both on a large scale – the new development of a system, for example – and on a smaller one – such as when we optimize existing lines and can have a big impact by making smaller changes, such as doing away with water lubrication. We are also working on various sensors which can assess the level of cleanliness in a system so that sanitizing cycles are only run until everything is clean and not according to a fixed time. Filtration systems can also recycle water to a great extent, again helping to keep fresh water consumption down to the absolute minimum.
Water savings on select KHS systems
At a production of | Annual water saving* (in liters) | How | |
---|---|---|---|
Can fillers** | Up to 70,000 cph | Up to 1.2 million l | Water-free roller lubrication, expansion joint instead of a sliding seal |
Tunnel pasteurizers | Up to 105,000 bph | Up to 25 million l | Speed control and cooling tower for maximum efficiency in the pasteurizer |
New bottle shower in glass bottle fillers | 50,000 bph | Up to 8 million l | New bottle shower development with respect to hygienic design |
ECO carrier bottle washer (also possible as an upgrade) | Up to 50,000 bph | Up to 32 million l | ECO carriers reduce heat and water consumption as they are designed in such a way that they carry over less heat and thus cut down on the amount of cooling water required. |
InnoPET BloFill stretch blow molder/filler block | Up to 36,000 bph | Up to 33 million l | Elimination of the PET rinser |
Mixer vacuum pump without sealing water | Up to 72,000 l/h CSD | Up to 1.2 million l | Constant temperature with its own cooling system as a closed circuit |
Glass beer bottle filler: vacuum pump | Up to 50,000 bph | Up to 31.8 million l | Constant temperature through an external cooling system |
* Calculation based on 6,000 hours of production per year
** This system is offered for small can fillers up to 70,000 cph. We also offer can fillers in the high performance range for up to 132,000 cph.
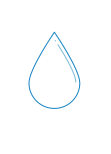
1.2 m L
Can filler
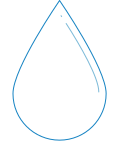
32 m L
Bottle washer
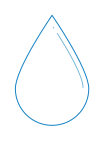
31.8 m L
Vacuum pump