A passion for service
Our products merely form the basis of a long period of cooperation with our customers. KHS is not only distinguished by its innovative spirit and demand for quality but also by its absolute conviction in the provision of service – both now and in the future. This becomes even more important when the objective is to help our customers to produce more sustainably.
The durability of our lines and machines is something which makes us proud and which conforms with our policies on sustainability. The flip side is that once the plant technology has reached a certain age, it is no longer state of the art – and thus no longer satisfies ideal requirements regarding energy efficiency and performance. This is where our concept of service comes into play which drives us in all sections of our company – especially when customers express the desire to save on resources.
From conviction we provide comprehensive advice on audits, conversions and upgrades to prevent the procurement of a new machine while maintaining the state of the technological art. Our dedicated KHS line optimization team individually tackles each separate inquiry. Working together in detail and in trust with the customer’s designated personnel we identify possible problems which occur when operating the line and which affect its performance.
To this end we make detailed studies, observations and measurements which enable us to find out where the snags in the line or process are. We then make specific suggestions as to how the line’s performance and energy efficiency can be improved. More and more customers are using this service because the results are well worth the effort.
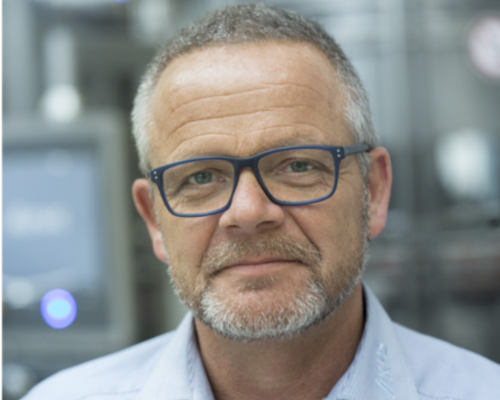
The devil is in the detail
It is important to take enough time to identify any problems and to trust in the experience of our expert team who work closely with the line operators. Problems often only become visible on closer inspection: in many cases the root of the problem does not lie with the large machines but in the little details which add up and influence the course of production. General organizational conditions may also affect the efficiency of line operation – but are usually never questioned. An outsider’s view can also help here. Sometimes very little things can have a big impact.
One good example here is the Pivovarna Union Brewery in Ljubljana, Slovenia, who are extremely satisfied with their cooperation with KHS. The KHS line optimization team first audited a returnable glass bottle line at the brewery. The resulting suggestions were then quickly implemented without exception by those responsible.
The result is that the filling system is now running much more efficiently than before. The suggestions also included a number of very simple measures, such as acquiring new electronic light barriers for the pallet lifts which with their frequent failures had caused repeated downtimes in production. Organizational aspects also played a role. KHS thus suggested staggering personnel lunch breaks so that production did not have to be interrupted for this purpose.
Whether the suggestions and recommendations made by the line optimization team are implemented or not is of course always up to the respective customer. What has proved its worth at all events, however, is the open, appreciative form of communication adopted by our service team and the customer’s designated personnel – with the full focus on sustainability.