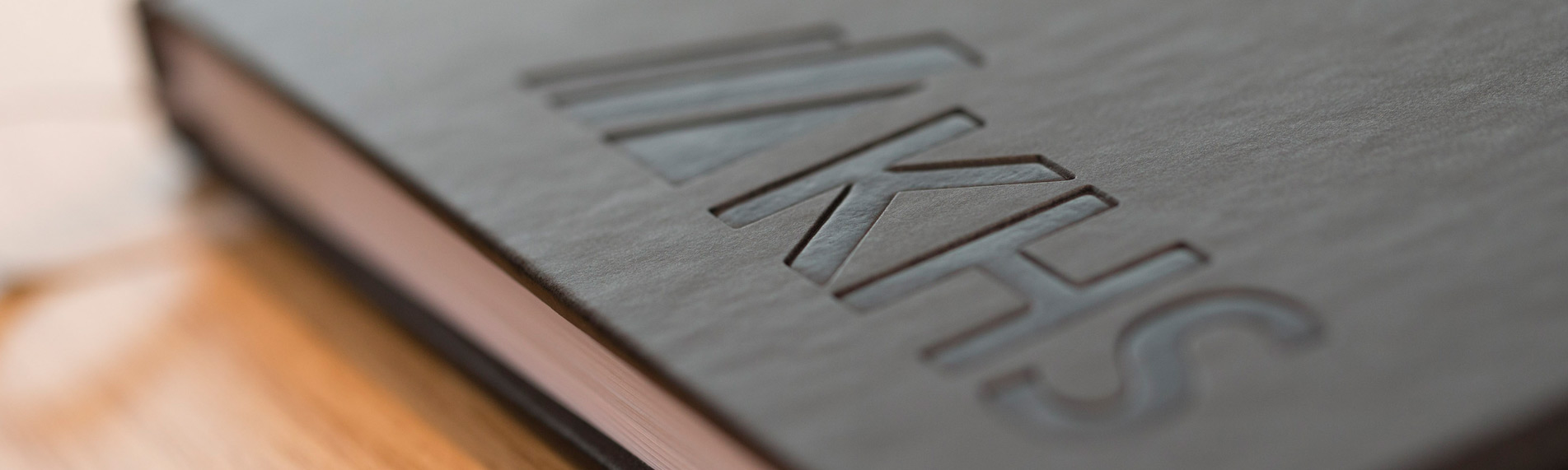
Anniversary for KHS Hamburg: 50 years of pioneering achievement and a strong team for the future
From the first stretch blow molder manufactured in series to Plasmax barrier technology: the KHS production site in Hamburg, Germany, is celebrating its 50th anniversary.
- Trailblazer in the development of sustainable PET systems and solutions
- Focus on recyclability and resource conservation
- Personnel commitment factor for success
Hamburg, July 17, 2025 – From the first stretch blow molder manufactured in series to Plasmax barrier technology: the KHS production site in Hamburg, Germany, is celebrating its 50th anniversary. The turnkey supplier looks back on half a century as a PET technology pioneer and wants to set standards in the future, too.
“Our factory in Hamburg is one of the pillars and drivers of the success and growth of the KHS Group,” says Kai Acker, CEO of KHS GmbH. “The last 50 years have shown just how much innovative strength this site has. Numerous systems and solutions developed in Hamburg still dominate the beverage and packaging industries today.”
PET technology pioneer
The company’s success story began in 1975 with the founding of Gildemeister Corpoplast GmbH, predecessor of the present KHS facility in Hamburg. With the first stretch blow molder manufactured in series, later known under the name of InnoPET Blomax, the business established competitive benchmarks in its branch of industry. Further key developments followed, among them groundbreaking Plasmax technology with its sustainable FreshSafe PET system and ultramodern lightweighting equipment.
The production site in Hamburg stands for resource-conserving plant engineering and sustainable packaging systems. All PET machines by KHS are able to process up to 100% recycled material. The containers these produce can thus be integrated into the closed bottle loop. What’s more, thanks to KHS technology customers can significantly cut their material and energy consumption. One example of this is the new generation of InnoPET Blomax stretch blow molders. Thanks to its optimized Double Gate heating system, it saves up to 40% in energy costs compared to single-lane stretch blow molders of the same capacity.
Hamburg’s field of specialization perfectly complements the network of proficiency established by KHS’ further facilities in Germany. The focus in Dortmund, for example, is on bottle washing, conveying and labeling technology plus manufacture, with Bad Kreuznach responsible for process engineering and filling technology, while Kleve concentrates on secondary packaging and Worms on palletizing systems. Together they ensure a holistic, innovative pool of system expertise.
Looking to the future
The PET market is growing worldwide. In order to meet the increased demand for resource-conserving packaging systems and smart production processes, KHS is expanding its factory in Hamburg. A new production shop and enhanced research facilities are being built. By investing in technology, infrastructure and specialist personnel, the plant is also safeguarding its powers of innovation for years to come. One pivotal factor here is the team in Hamburg, emphasizes Acker. “Our employees are the key to our success. Their expertise and unparalleled commitment considerably help to ensure that we’re able to flourish on a global scale.”
Kai Acker (Source: Frank Reinhold)
“Our factory in Hamburg is one of the pillars and drivers of the success and growth of the KHS Group,” says Kai Acker, CEO of KHS GmbH.
Download image (JPG, 78 KB)Hamburg site, Germany (Source: Frank Reinhold)
The production site in Hamburg stands for resource-conserving plant engineering and sustainable packaging systems.
Download image (JPG, 108 KB)InnoPET Plasmax (Source: Rüdiger Sternal)
Pioneering achievement from Hamburg: with its Plasmax technology, KHS sets standards in sustainable barrier technology for the protection of sensitive products.
Download image (JPG, 42 KB)FreshSafe-PET (Source: Frank Reinhold)
FreshSafe PET coating technology from KHS combines highly effective product protection with 100% recyclability by material type.
Download image (JPG, 114 KB)InnoPET Blomax (Source: Frank Reinhold)
Thanks to its optimized Double Gate heating system, the latest machine generation saves up to 40% in energy costs compared to single-lane stretch blow molders of the same capacity.
Download image (JPG, 128 KB)