Available soon: Innofill PET ACF-R
Filling of sensitive beverages into PET bottles
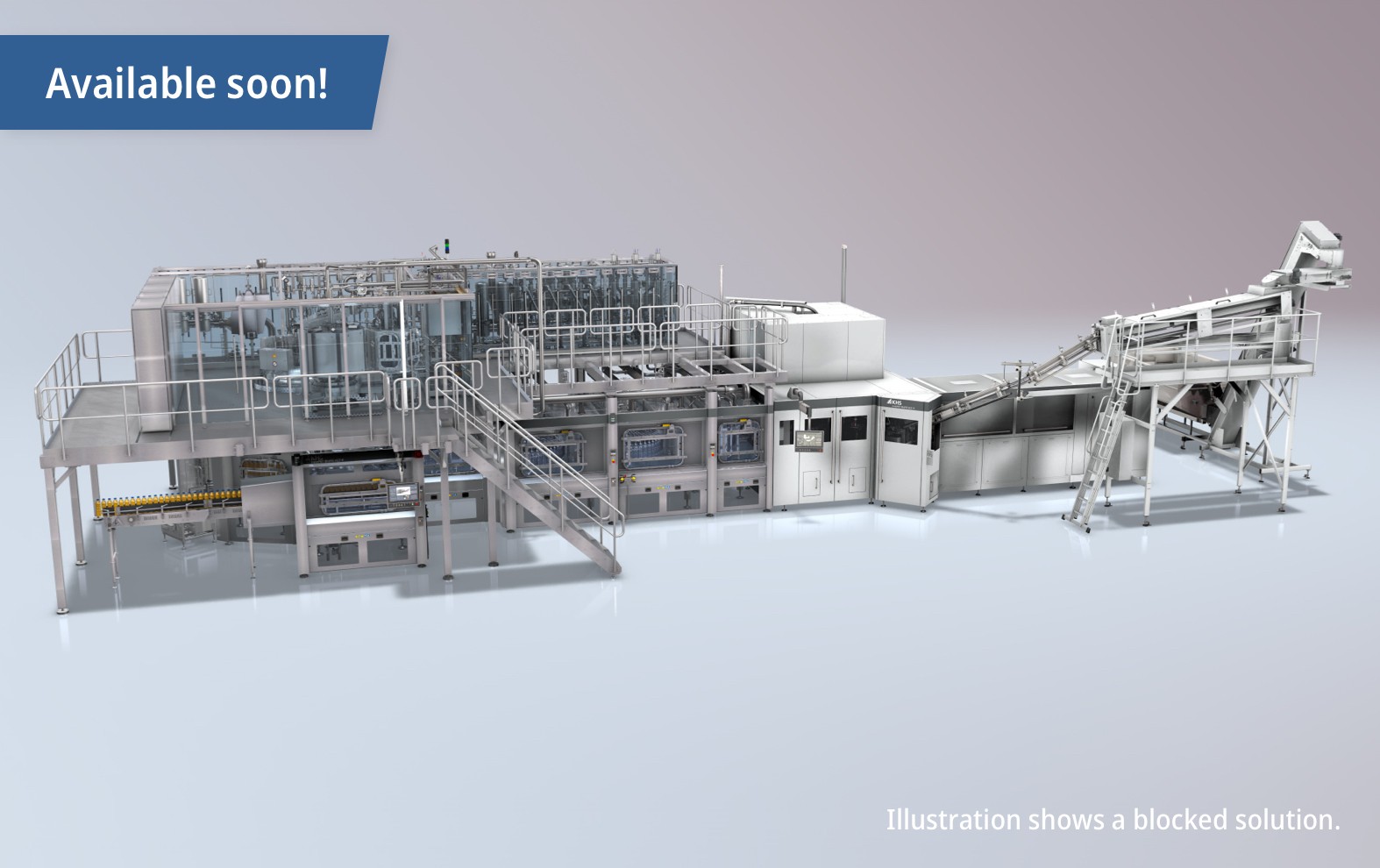
Good to know
Our systems enable aseptic filling of sensitive low- and high-acid beverages into PET bottles. Thanks to dry sterilization with hydrogen peroxide, germ reduction rates of up to log 6 are achieved for both bottles and caps. Our systems can be used in conjunction with air conveyors and Blomax stretch blow molders. The hygienic servocapper with vertical and rotary servomotors provides first-class capping quality. The compact design of our machines results in short processing segments and small aseptic zones. Outputs of 16,000 to 48,000 bottles per hour give you a wide capacity range for different production requirements.Your capacity requirements for 1.0-liter containers can be met by a throughput of up to 36,000 bottles per hour, for example.
Well thought out
Our systems have a sophisticated sterile air management system for maximum aseptic safety. Your production process is optimized by short product paths and quick product changeovers ensured by the integrated service module.
Non-contact, free-flow filling is suitable for sensitive beverages, with a pressurized filling option available for carbonated beverages.
Our servocapper stands for reliable quality with each and every cap. A monitored H2O2 liquid lock circulation system for the filler carousel and capper ensures constant sterility during the filling process.
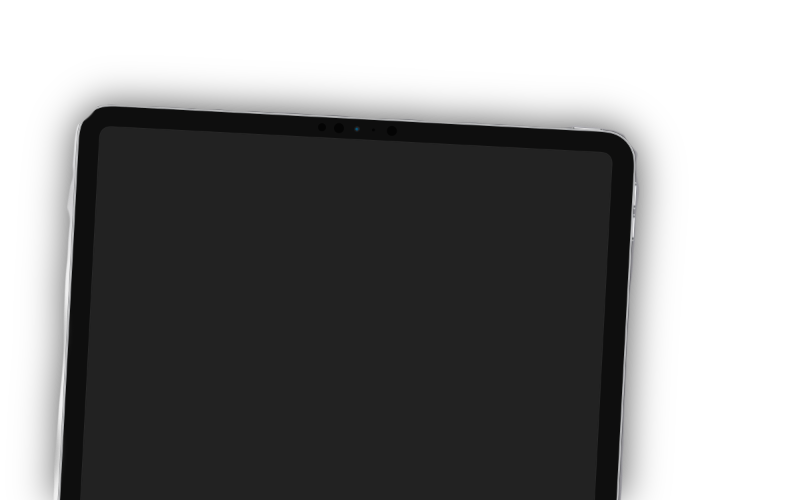
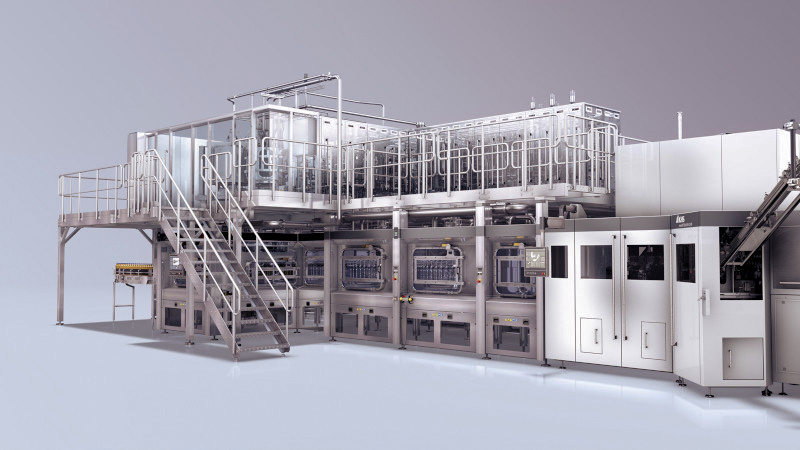
Further reading
High capacity, greater safety
Thanks to its rotary filler the new KHS aseptic block for bottle sterilization provides three times the capacity of the linear variant.
Learn moreConvincing
- Less than 0.5 ppm H2O2 residue in the bottle after 24 hours
- Small aseptic zone
- Reduced number of transfer stars during bottle sterilization
- Gentle filling with three switchable filling speeds
- Short processing segments thanks to integrated process components and a service module on the platform.
Sustainable
High line availability is ensured by the following:
- Automatic product changeovers in 30 minutes
- Automatic format changeovers with the same neck
- Optional: short intermediate sterilization with peracetic acid in just 15 minutes
- Greatly reduced CIP/SIP times thanks to simultaneous cleaning of the product paths and aseptic zone.
Consumption is considerably minimized by the closed circuit and reuse of cleaning media. No separate foaming station or foam cleaning is thus needed. Our efficient cleaning technology not only optimizes consumption; it also greatly reduces the amount of cost and effort required for the cleaning process.
The machine will also be available as a blocked solution in combination with our stretch blow molder InnoPET Blomax Series V.
Note on the image: The rendering depicts the blocked solution and may still change before publication.