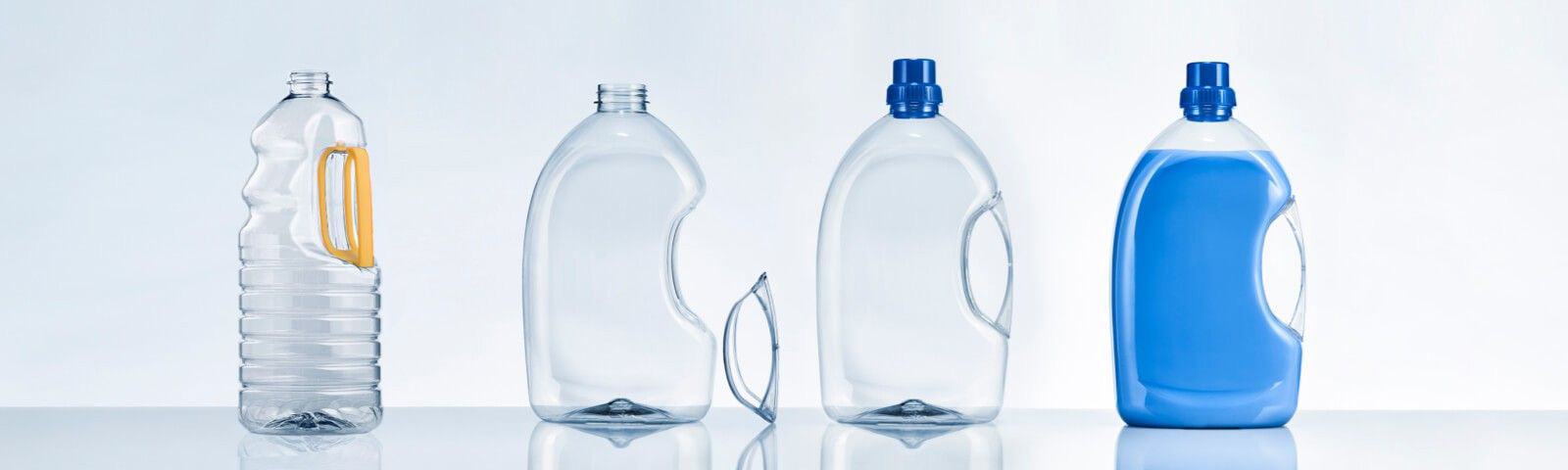
Clipped or glued: integral grip systems made of [r]PET promote circularity
With a stable handle you can now offer your food and home care products in large, round and oval [r]PET containers that make the product extremely convenient to use. An integral clip-in or glued-in handle gives your customers ergonomic bottle handling, saves on material and is very stable. By using [r]PET you also enable your container to be fed to the closed recycling loop.
Whether used for cooking oil, sauces or liquid detergent, containers with a filling volume of over 1.5 liters are that much heavier and must be safe and convenient for the consumer to transport. The polypropylene and HDPE materials commonly used for such bottles may be easy to handle but have the disadvantage that, unlike [r]PET, they cannot be used in a circular economy.
Sustainable and efficient production process
Recycled PET is a hot topic at the moment for good reason and is being increasingly used to make high-quality bottles.
The production process has a number of major economic advantages: the line efficiency is extremely high for the inline production of [r]PET containers including handle application. In this process the containers run straight from manufacture to filling, whereas in offline manufacture they are produced as stock, resulting in additional warehouse stockpiling or sometimes even a surplus of containers. With [r]PET containers with appropriate handles you therefore also profit from secondary benefits in logistics, warehousing and the use of space. Here, tried-and-tested KHS InnoPET Blomax Series V stretch blow molder technology stands for low energy consumption, high production efficiency and stable process reliability. In the production of containers with clip-in handles, this plant engineering proves especially convincing with the maintenance-friendly design of the required mold-moving sections during the bottle blowing process; compared to competitor machines, this results in a much longer service life and thus takes up less maintenance time and incurs fewer costs. Alternatively, the grip can be fixed with the help of our new Innopack Nature MultiPack adhesive specially developed for this application. This further reduces the amount of material used in the bottle and even makes the mold-moving sections usually needed to form the pockets for the clip-in handles superfluous.
Good to know
With its combination of container design expertise and know-how in packaging innovation KHS is now launching a unique new system to market: an oval bottle with a glued-in handle for home care applications. Both the bottle body and injection-molded handle are made of 100% [r]PET and thus help to make the bottle fully circular as the adhesive can also be recycled. This is a milestone in the striving towards a circular economy for household products!
Lightweighting possible
Furthermore, material is saved by the properties of the PET itself: as this hardens automatically in the stretch blow molding process, considerably less material is needed per container than with HDPE, where the same degree of stability can only be achieved using a far greater amount of material. [r]PET therefore enables lightweight containers with very stable handles to be produced. While blown grips can split at the seams if subjected to heavy loads, our handle options are extremely stable and easy and pleasant to handle.
Energy efficiency at the plant
By saving on material, costs and energy consumption, in opting for [r]PET with clip-in or glued-in handles you have a lower total cost of ownership (TCO) and produce fewer emissions that are harmful to the climate. This is a significant plus as low-emission production is very important to most companies.
Quick changeovers possible
You can switch to [r]PET and implement your own individual, recyclable container system in a very short time indeed. Changeovers to a different color on the line also take just a few minutes: the preform is simply exchanged directly as and when required, whereas changing colors on HDPE extrusion blow molders can take several hours.
Interested? Then please feel free to contact us directly! We’d be happy to personally advise you – with no further commitment – on your future bottle design, materials, production process and machine delivery. Service is always writ large at KHS!